Quality Assurance (QA) is a monitoring approach that evaluates various aspects of an acquisition project, or service to determine if the minimum standards of quality are being attained by the production process. QA includes regulation of the quality of raw materials, assemblies, products and components, services related to production, and management, production, and inspection processes. The International Organization for Standards (ISO) defines QA as a part of Quality Management focused on providing confidence that quality requirements will be fulfilled.
Definition: Quality Assurance is the maintenance of a desired level of quality in a service or product, especially by means of attention to every stage of the process of delivery or production.
Quality Assurance (QA) Principles
The two (2) principles included in QA are:
- “Fit for purpose” – the product should be suitable for the intended purpose
- “Right first time” – mistakes should be eliminated
Quality Determination
Quality is determined by the product users, clients, or customers. It’s not the same as ‘expensive’ or ‘high quality. Low-priced products can be considered as having high quality if the product users determine them as such. [1]
Quality Assurance (QA) Process and the Continuous Improvement Process (CIP)
The Quality Assurance (QA) Process mirrors the Continuous Improvement Process (CIP) which is an ongoing effort to improve products, services, or processes. It’s is a six-step systematic approach to plan, sequence and implement improvement efforts using data and elaborates on the Shewhart Cycle (Plan, Do, Study Act). The CIP provides a common language and methodology which enables understanding the improvement process. The CIP always links back to each organization’s own goals and priorities.
Definition: Continuous improvement is the act of continually looking to improve upon a process, product, or service through small incremental steps.
Why Use a Continuous Improvement Process (CIP) for Quality Assurance (QA)
Implementing a Continuous Improvement Process in an organization should be standard practice now. Studies have shown the main benefits of a QA are:
- Greater customer satisfaction
- Cost reduction
- Increase productivity
- Better teamwork and morale
- Greater agility
- Less waste
- More efficiency
- Increase customer satisfaction
- Increase in profit
Phases of the Continuous Improvement Process (CIP)
There are four phases associated with the CIP that a Quality Assurance (QA) Process follows. These phases are associated with the Shewhart Cycle:
- Phase 1 “Plan”: Plan for change and identify improvement opportunities.
- Phase 2 “Do”: Implement changes identified.
- Phase 3 “Study”: Check to determine if the change had the desired outcome.
- Phase 4 “Act”: If successful, implement across the organization and process.
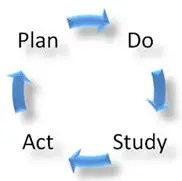
Six (6) Steps of a Quality Assurance Process
- Step 1: Identify Improvement Opportunity: Select the appropriate process for improvement.
- Evaluate Process:
- Select a challenge/problem
- Step 2: Analyze: Identify and verify the root cause(s).
- Step 3: Take Action: Plan and implement actions that correct the root cause(s).
- Step 4: Study Results: Confirm the actions taken to achieve the target.
- Step 5: Standardize Solution: Ensure the improved level of performance is maintained.
- Step 6: Plan for the Future:
- Plan what is to be done with any remaining problems
- Evaluate the team’s effectiveness Set a target for improvement
Quality Assurance (QA) Development Cycle [1]
The Best Time to Start a Quality Assurance Process
There is no bad time to start using plan a continuous improvement process but the sooner the better. Below is a list of the times I believe a QA should be implemented:
- Beginning of a new project
- Development of processes and procedures
- Developing a new or improved product, or service
- Planning data collection and analysis
- Implementing any change to a process
- Whenever a failure occurs
Tools that can be used to help with Quality Assurance (QA) are:
- Benchmarking
- Force Field Analysis
- Flowcharts
- Affinity Diagram
- Delphi Technique
- Pareto Chart
- Cause and Effect Diagram
- Scatter Diagram
- Check Sheet
- Control Chart
- Process Capability Index and Ratio
- ISO 14000
Quality Assurance (QA) Surveillance
One of the quality assurance activities is surveillance. Surveillance is an on-going verification that a contractor’s quality system meets contract quality requirements and produces quality products. In accordance with Program Management Office and buying activity requirements, the Defense Contract Management Agency (DCMA) field activity surveillance:
- Identifies critical processes
- Develops and maintains a written risk-based surveillance plan
- Performs necessary surveillance
- Performs data analysis
Quality Management Plan (QMP)
Quality Assurance (QA) should be addressed in the Quality Management Plan (QMP). The QMP helps guides the Program Manager (PM) and project personnel to execute quality management and quality assurance activities for a project or program. The QMP is normally developed by a contractor and reviewed by the customer. Quality is the degree to which the project fulfills requirements.
Definition: Quality Management is the act of overseeing all activities and tasks that must be accomplished to maintain a desired level of excellence. This includes the determination of a quality policy, creating and implementing quality planning and assurance, and quality control and quality improvement.
Quality Assurance (QA) Audits
Government Contract Quality Assurance (GCQA) determines if contractual requirements have been met prior to acceptance of supplies and services by Quality Audits. GCQA is conducted by the program manager and DCMA as identified in contract administration delegations to DCMA by the Contracting Officer.
AcqTips:
- QA cannot absolutely guarantee the production of quality products.
- The Defense Contract Management Agency (DCMA) is responsible for contract quality assurance along with the program office
AcqLinks and References:
- Defense Acquisition Guidebook (DAG) – Chapter 11
- Website: FAR Part 46 “Quality Assurance”
- [1] Website: Wikipedia – Quality Assurance
Updated: 7/14/2021
Rank: G34