The “Controlling Process” is a method that can ensure standards are being met within an organization. It involves the careful collection of information about a system, process, person, or group of people in order to make necessary decisions about each. The act of controlling is considered crucial in the management process. The entire management process will be rendered useless without some control mechanism. Without accurate metrics, management cannot tell if their plan is effective or if it is being carried out as intended. For a business to stay in business, controlling management is an important process. You can tell what works and what doesn’t work when you keep an eye on and manage the production process. The process typically has between 4 and 5 steps. (See Below)
Definition: “Controlling” assures that the right things are done in the right manner at the right time. By controlling, a Program Manager checks the progress and compares it to what was planned. If the planned events are not the same, then corrective actions can be taken.
Purpose of the Controlling Process
The main purpose of the control process is to ensure that all of an organization’s actions are going according to plan. The control process helps managers determine how well their organizations are doing and what is working and what isn’t.
Controlling Process Steps
To set up, track, and improve your business activities, whether production, packaging, shipping, or something else, there is a five-step process for controlling them. A five (5) step-controlling process is listed below, with an example at the end.
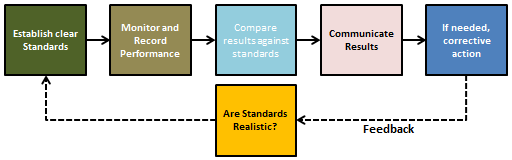
-
- Measurable or tangible: Those standards that can be measured and expressed are called measurable standards. They can be in the form of cost, output, expenditure, time, profit, etc.
- Non-measurable or intangible: Some standards cannot be measured monetarily. For example- a manager’s performance, the deviation of workers, and their attitudes towards a concern. These are called intangible standards.
- Controlling becomes easy through the establishment of these standards because controlling is exercised based on these standards.
Step 2: Monitor and Record Performance: The second major step in controlling is to measure the performance. Finding out deviations becomes easy by measuring the actual performance. Performance levels are sometimes easy to measure and sometimes difficult. Measurement of tangible standards is easy as it can be expressed in units, cost, money terms, etc. Quantitative measurement becomes problematic when a manager’s performance has to be measured. The performance of a manager cannot be measured in quantities. It can be measured only by:
-
- The attitude of the workers,
- Their morale to work,
- The development in attitudes regarding the physical environment and
- Their communication with the superiors.
Step 3: Comparison Results Against Standards: Comparison of actual performance with the planned targets is very important. The deviation can be defined as the gap between actual performance and the planned targets. The manager has to find out two things here- the extent of deviation and the cause of deviation. The extent of deviation means that the manager has to find out whether the deviation is positive or negative or whether the actual performance is in conformity with the planned performance. Once the deviation is identified, a manager has to think about various causes that have led to it. The causes can be:
-
- Erroneous planning,
- Co-ordination loosens,
- Implementation of plans is defective, and
- Supervision and communication are ineffective, etc.
Step 4: Communicate Results: All stakeholders need to be notified and updated once the results have been determined.
Step 5: If needed, Take Corrective Action: Once the causes and extent of deviations are known, the manager must detect those errors and take remedial measures. There are two alternatives here:
-
- Taking corrective measures for deviations that have occurred and
- After taking corrective measures, the manager can revise the targets if the actual performance does not conform to plans. It is here the controlling process comes to an end. Follow-up is an important step because it is only through taking corrective measures a manager can exercise control.
Controlling Process Example
The following is an example of a Project Manager (Sarah) utilizing the controlling process for a High-Rise Office Building Construction.
- Step 1: Establish Clear Standards: The first step in any project is for the program manager, Sarah, to establish control measures that align with the project’s goals. Key performance indicators (KPIs) include cost performance, timetable adherence, quality metrics, and safety records are examples of what might be considered.
- Step 2: Monitor and Record Performance: Sarah reviews reports, travels to job sites, and regularly communicates with the various project teams to keep tabs on how things are going with the building project. She keeps the project on track and ensures that goals and deliverables are accomplished.
- Step 3: Comparison Results Against Standards: Sarah examines any discrepancies between actual results and the anticipated goals and baseline during the process of controlling. If, for instance, actual building costs end up being more than planned, she’ll figure out why, pinpoint any associated risks, and implement solutions.
- Step 4: Communicate Results: Informing Stakeholders and Giving Updates are part of the process; Sarah updates those who need to know about accomplishments, setbacks, and course corrections. She regularly updates on the status of the project, focusing on the most important KPIs, any discrepancies, and how well the corrective actions are working. This allows interested parties to maintain their knowledge and make educated choices. Sarah routinely updates the project plans by considering the findings from the study of deviations and corrective actions. If necessary, she revises the program’s goals, milestones, budgets, and timelines to reflect the present state of the project and assure the program’s continued viability and success.
- Step 5: Takes Corrective Action: Sarah takes corrective efforts to get the project back on track whenever she notices a variation or variance. If the construction timetable is running behind, she may decide to bring in more help, move up the project’s start date, or try out some new approaches to getting things done.
Sarah, as Program Manager, can be more proactive in her management of the construction schedule, as well as the identification and resolution of problems, thanks to the controlling process. As a result, she can keep the project under her control, keep it on track financially and time-wise, and help the high-rise office building project succeed as a whole.
Understanding Deviation in the Controlling Process
Deviation is the difference between what happened and what should have happened. Deviation can be both positive and negative.
- Positive Deviation: The performance is better than the normal performance, which is a type of deviation called positive deviation.
- Negative Deviation: This type of deviation happens when the real performance is lower than the expected performance.
Difference Between Planning and Controlling
Planning and Controlling are two different management tasks, but they are closely related and depend on each other. Their tasks often cross, and they depend on each other to do their jobs well.
- Planning is the basis for keeping things under control. Setting goals, defining targets, and figuring out how to reach them are all part of planning. It sets up the organization’s road map by listing the tasks, resources, and deadlines that will be needed. Without good planning, a company lacks direction and clarity, which makes it hard to reach its goals.
- Controlling, on the other hand, means keeping an eye on progress, comparing performance to already set standards, and making changes when needed. It makes sure that everything goes as planned and that any problems are found and fixed. Controlling helps keep things working well and in line with the organization’s goals. Without managing, planning is just a thought experiment because there is no way to tell if the plan is being carried out well.
Planning and controlling can be considered a feedback process that keeps going and going. Planning sets goals and standards, and controlling gives you a way to track your progress and make changes as needed. Controlling gives feedback to planning by showing where things could be better, pointing out where there are gaps, and giving information for future planning processes.
Planning and Controlling also have some things in common and use some of the same tools and methods. For example, setting goals, allocating resources, and analyzing data are all part of both roles. To make sure that organizational actions go well, they need to communicate, coordinate, and make decisions well.
Even though planning and controlling are two different management parts, they are closely related and depend on each other. Planning lays the groundwork for controlling, and controlling gives feedback and helps plan for the future. For the company to reach its goals and keep a strategic advantage, it is important that both functions work well.
AcqLinks and References:
- [1] Nickels and McHugh, “Understanding Business” McGraw-Hill Irwin 2010
Updated: 3/19/2024
Rank: G5.9